Concrete plays a big role in planet-warming emissions. It’s the world’s most common synthetic material and most-consumed resource besides water.
Along with other environmental and health impacts, concrete generates as much as 8 percent of all CO2 emissions, mostly from its key ingredient, cement. Indeed, if the cement sector were a country, it would be the world’s third-biggest CO2 emitter.
An array of Finnish firms and researchers are working to turn concrete from a climate problem into a solution for carbon storage.
The market for such carbon-negative “green concrete” is set to grow rapidly, as it could be a crucial building block for lowering emissions. The Global Cement and Concrete Association, which includes the world’s biggest companies in the sector, has committed its members to being net zero by 2050, and laid out a detailed roadmap to do so.
Some of the technologies to reach that end are now being cooked up in Finnish labs in hopes of grabbing part of the market.
Active R&D
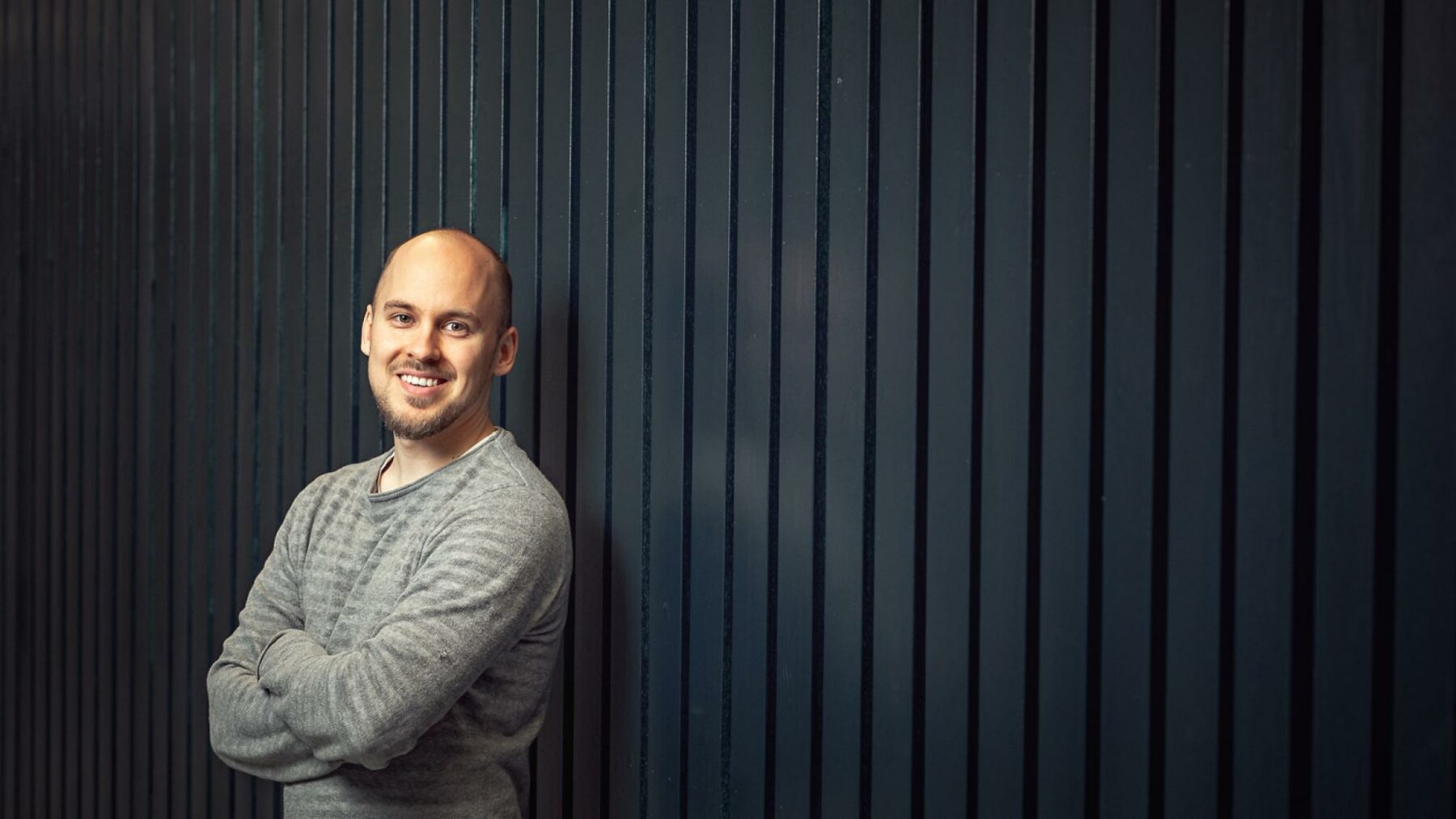
“A lot of companies are taking this seriously and developing it forward,” says University of Oulu associate professor Juho Yliniemi about lower-carbon cement and related materials.Photo: University of Oulu
“There’s quite active R&D going on in green concrete and cement in Finland,” says Juho Yliniemi, associate professor of fibre and particle engineering at the University of Oulu. Besides his own institution, he points to work at Lappeenranta-Lahti University of Technology and Aalto University and about ten companies.
These include Carbonaide, which uses the concrete curing process to lock in carbon, in a process developed at the VTT Technical Research Centre of Finland.
“With our approach, we’re able to mineralise significant amounts of carbon dioxide into concrete as permanent storage in a very simple and cost-effective setup,” says Niina Haapasalo, Carbonaide’s chief technology officer. “Through the curing process, we can maximise the mineralised CO2 and minimise the amount of cement needed.”
She explains, “The two important targets have been a low threshold for industrial usability, and CO2 mineralisation amounts that are climate-significant. We found that concrete curing was just a perfect place, production-wise, to implement our process easily and impactfully at existing concrete plants.”
Construction materials as a carbon sink
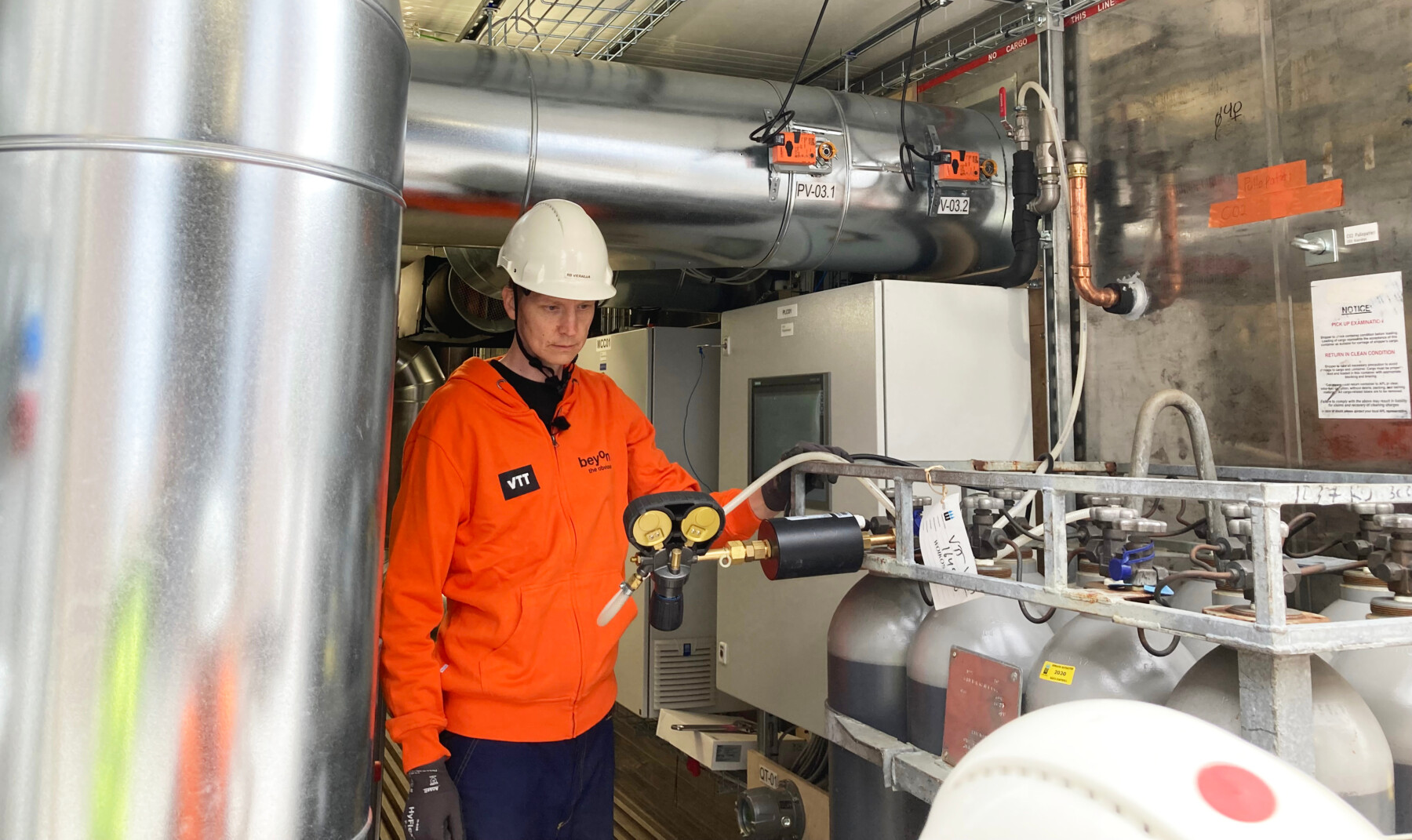
Carbonaide CEO Tapio Vehmas checks equipment at a plant in Hollola, southern Finland.Photo: Vesa Kippola/VTT
The company’s first carbonated products are slated for a spring 2024 launch by a partner, with delivery of full units beginning later in the year.
“Our goal is to create a more sustainable future with cutting-edge tech that doesn’t just reduce the carbon emissions of construction materials like concrete, but traps more CO2 than they emit throughout their lifetime,” says Carbonaide CEO Tapio Vehmas. “It’s very natural that the constructed environment becomes a CO2 sink, as it’s the largest volume of man-made material.”
The amount of carbon that the product sequesters can readily be verified through lab tests, generating data that partner companies can use in calculating their own climate footprints.
“The amount of carbonised CO2 is based on our process calculations, which are validated by lab measurements by a third party,” says Haapasalo. “On the commercial scale, all the mineralised CO2 is analysed in two ways, so it’s absolutely transparent.”
Helsinki demands low-carbon concrete
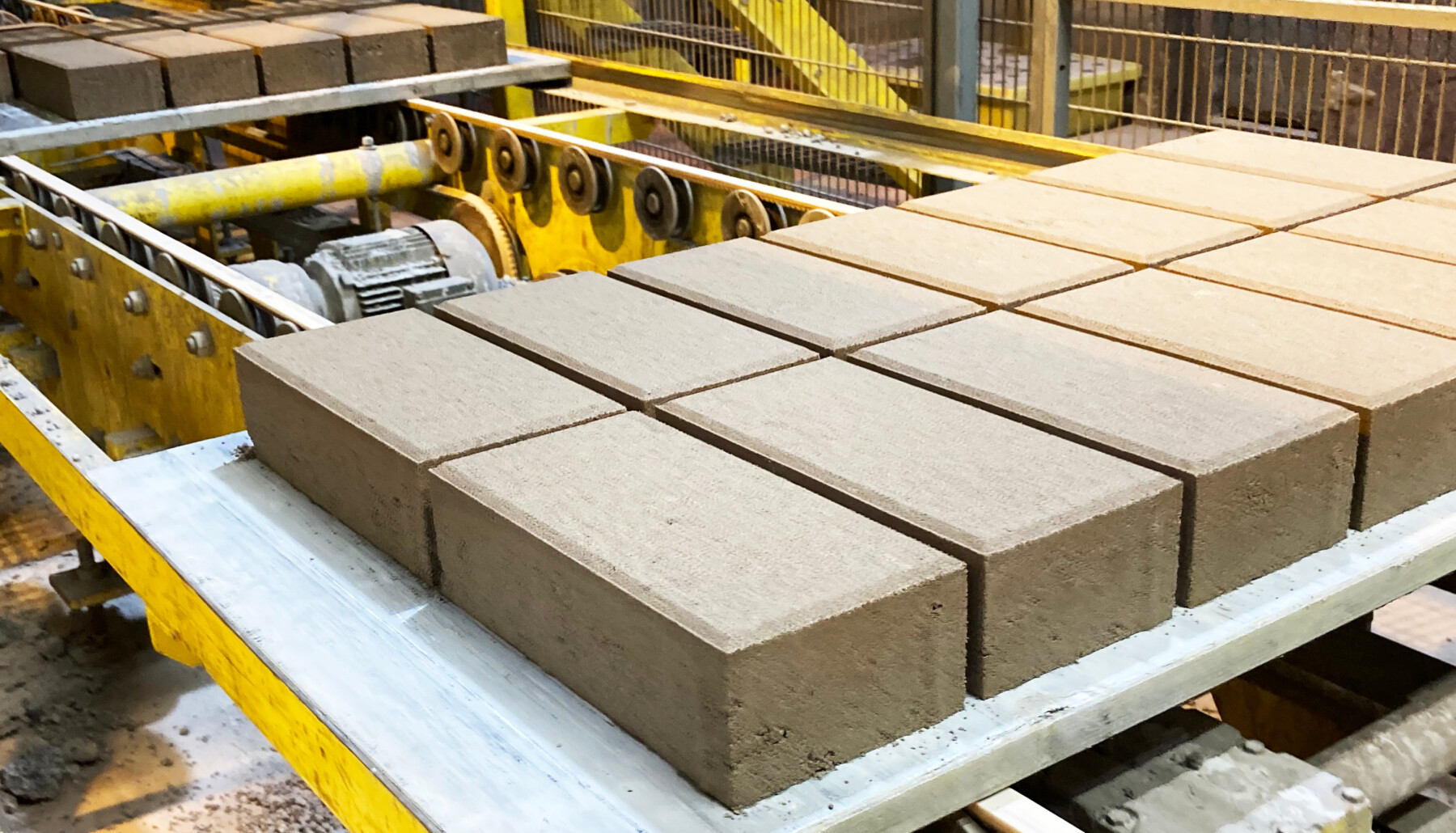
It appears that product innovation and commercial demand have arrived in the same place at the same time.Photo: VTT
Verified data is essential for commercial adoption. For instance, in 2023, Helsinki began requiring that low-carbon concrete be used in all city-commissioned infrastructure projects, with a standard defined by the Concrete Association of Finland that will become stricter each year.
“Some big concrete companies are creating low-CO2 cement by mixing blast-furnace slag with their cement as their main supplementary cementitious material,” says Yliniemi.
Finland’s biggest concrete manufacturer, Parma, offers green concrete that promises to lower CO2 emissions by 40 percent, while its main rival, Rudus, claims that its version can cut emissions by as much as 60 percent compared to standard concrete.
Another big firm, Suutarinen, announced plans in early 2024 to build the country’s biggest concrete element factory in Mikkeli, with products made using the firm’s own low-carbon material.
Meanwhile, several smaller firms are using mineral sidestreams – typically waste materials – to craft cement-like binding agents known as geopolymers that have a smaller carbon footprint and can even perform better.
These firms include Betolar, founded in 2016, with former Nokia CEO Olli-Pekka Kallasvuo serving as its advisor, and EcoUp, which upcycles waste mineral wool into a binder for geopolymer concrete. Another is Keko Geopolymeerit, which Yliniemi cofounded in 2020, focusing on alkali-activated materials.
“There seems to be a high push and pull in the construction industry,” says Yliniemi. “A lot of companies are taking this seriously and developing it forward, so it’s going to happen. It’s quite a conservative industry, though, so things always take more time than expected. But I’m optimistic at the moment.”
By Wif Stenger, April 2024